HDrive17-ETH
Your imagination defines the possibilities — not the limitations of a PLC.
Leverage the flexibility and scalability of the system through your own programming expertise.
No need to rely on third-party tools or proprietary PLC IDEs — you stay in full control.
Engineered for Maximum Reliability and Longevity
The HDrive17-ETH-i is meticulously engineered to deliver exceptional reliability and an extended service life. Every unit is handcrafted in Switzerland, ensuring the highest quality standards are met.
Each drive undergoes comprehensive calibration and rigorous testing to guarantee optimal performance from day one.
To support both sustainability and economic efficiency, we source all components for the HDrive17-ETH-i from the closest and most cost-effective suppliers—primarily within Europe.
Integrated Web Server – Control Made Simple
The HDrive17-ETH-i features a built-in web server, allowing you to configure, monitor, and control your entire drivetrain system directly through an intuitive web interface.
Thanks to live visualization, you receive real-time feedback on system performance—accessible from any web browser, whether you’re on a mobile device or desktop computer, even while the drive is running.
No additional software or apps are required. Simply open your browser and you’re ready to go.
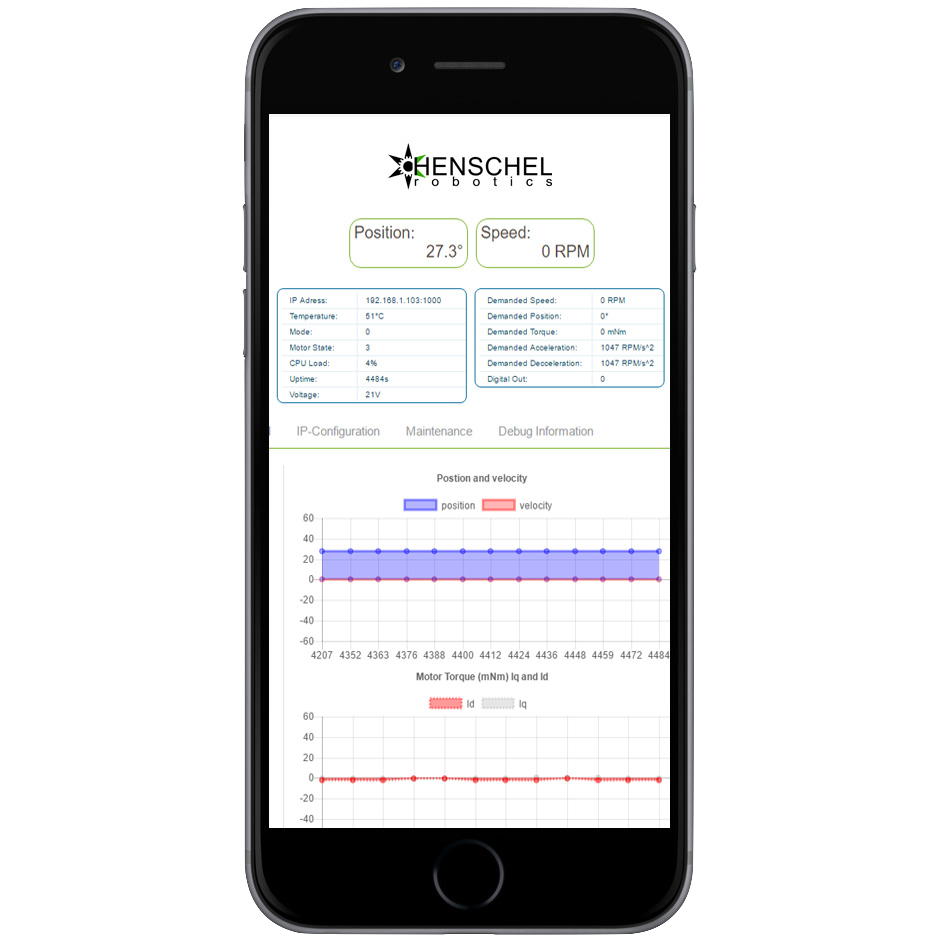
Sophisticated control
Hightech
At the core of the HDrive is a state-of-the-art ARM microcontroller, paired with high-precision sensors for accurate position and current measurement. This advanced hardware foundation ensures exceptional performance, responsiveness, and reliability in every application.
Jerk free motion
Thanks to a sophisticated Field-Oriented Control (FOC) algorithm, the motor operates with ultra-smooth motion and precise torque control. The result is performance that matches that of traditional DC servo motors, with minimal vibration and maximum efficiency.
7 state motion planer
The integrated 7-state path planner allows independent adjustment of acceleration, deceleration, and speed, giving you full control over motion dynamics. It continuously calculates the optimal trajectory in real time, adapting to the motor’s current state to ensure smooth, efficient, and precise movement at all times.
Attach up to 8 slave motors.
Every HDrive can operate as either a CAN master or slave, offering maximum flexibility for system integration.
When configured as a CAN master, the HDrive17-ETH-i automatically sets up a local CAN network. All connected slave drives are automatically detected—no manual configuration required.
You don’t need to worry about internal communication. The master receives commands via Ethernet and seamlessly distributes them to all slave units.
A synchronization signal ensures that motion is simultaneously triggered across the entire network, enabling precise, coordinated movements.
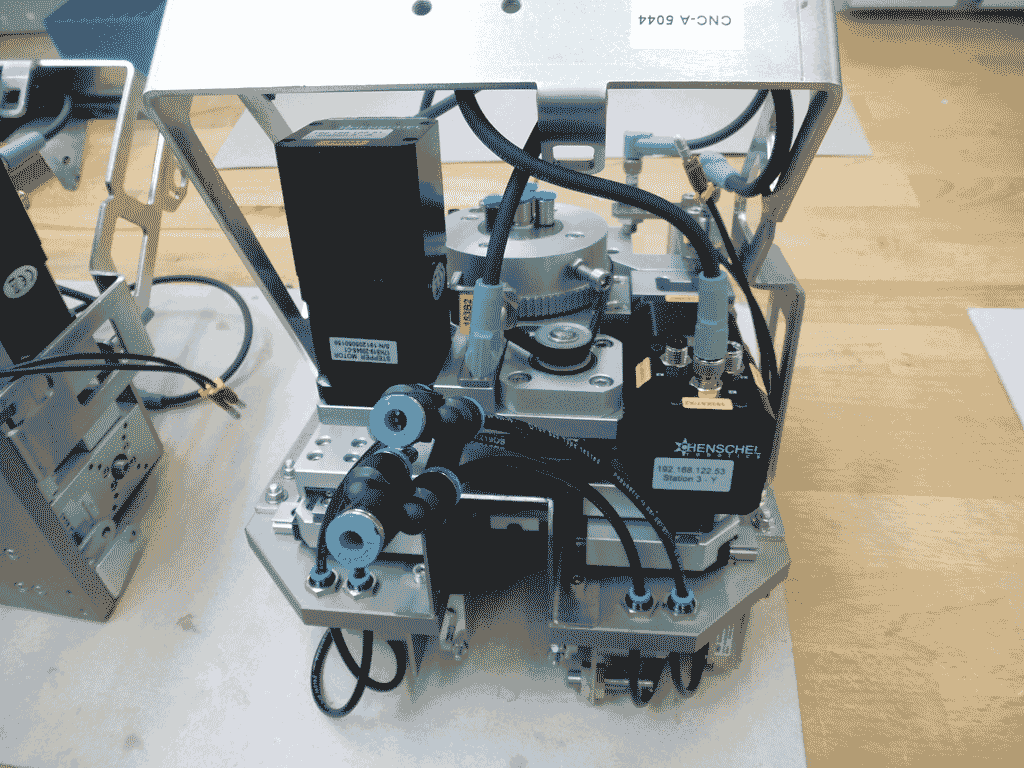
Everything integrated.
A conventional servo motor is made out of multiple parts. The user needs to setup, wire and configure everything.

The HDrive does only need an Ethernet capable device on the host side. A PC is sufficient, only plug the power and the ethernet and your setup is done

Simple and Powerful Command Interface
Controlling the HDrive17-ETH-i is straightforward. For example, the following command sets a new target position of 20.2°, with a maximum speed of 300 RPM, acceleration and deceleration of 1000 RPM/s, and a torque limit of 150 mNm:
<control position=”202″ speed=”300″ torque=”150″ mode=”129″ acc=”1000″ decc=”1000″ />
This XML-based interface allows you to program even complex motion sequences with just a few lines of code. Almost any modern programming language can send these commands over TCP/IP, making integration into your application fast and easy.
For higher performance and enhanced security, a binary protocol is also available—ideal for soft real-time or resource-constrained applications.
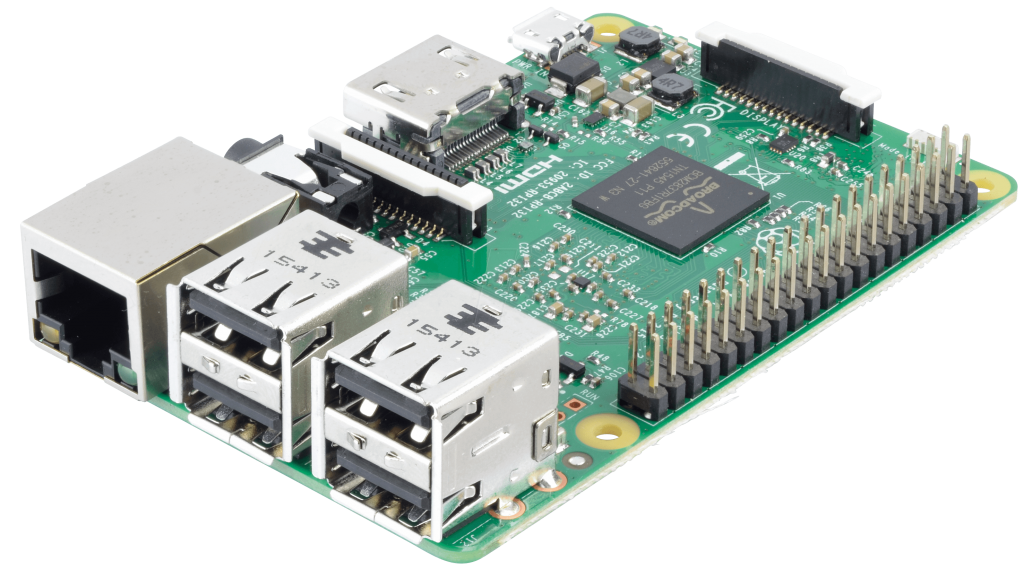
Universal Ethernet Connectivity – No Drivers Required
You can control the HDrive Servo Motor using virtually any Ethernet-capable device—no special drivers or OS dependencies required.
Whether you’re using an Arduino with Ethernet shield, Raspberry Pi, BeagleBone, industrial PC, or a standard desktop computer, the HDrive17-ETH-i integrates seamlessly over TCP/IP.
This makes it ideal for everything from rapid prototyping to full-scale industrial automation.