About us
The Henschel-Robotics GmbH is an innovative robotics startup domiciled in Winterthur, Switzerland. Currently we are working in a small team out of industry experienced researchers and senior hardware engineers.
Mission
Our mission is to push the boundaries of servo drive technology by delivering extremely power-efficient integrated servo drives with built-in Ethernet and EtherCAT connectivity. We strive to extract every bit of performance from the motor, providing the most efficient and powerful solutions possible.
Innosuisse Project: Advancing Field Weakening in Stepper Motors
January 21, 2025
We are excited to share that we have successfully completed an Innosuisse project focused on exploring the field weakening process in stepper motors. Through our lab tests, we achieved motor speeds of over 3000 RPM using this innovative approach. Building on these promising results, we’re preparing to integrate this breakthrough into our products and will release it as part of an upcoming firmware update. Stay tuned for more details on how this enhancement will boost the performance and efficiency of your servo drive solutions.
Read moreEtherCAT and EtherCAT-P
September 16, 2023
Henschel-Robotics GmbH is pleased to announce the forthcoming release of our advanced Nema17 Sized Servo Drive, complete with EtherCAT-P capabilities. This innovative product is engineered to deliver exceptional performance while eliminating the necessity for a separate PLC system. Further details will be disclosed shortly; we invite you to stay connected for this pivotal advancement in the industry.
Read moreNema23 Servo with up to 2.5 Nm stall torque
September 25, 2021
Soon we will release a novel power stage for our HDrive which is capable to drive bigger motors with a total current of up to 10A continuously. This power stage will be used in our Nema23 and Nema24 motors. This development will also enable tests with much bigger motors like the Nema34 or Nema42. The release date is scheduled to the end of 2021.
Read moreRipple current compensation
July 6, 2019
A beachelor thesis at the zuerich university of applied science (ZHAW) has been made by M. Bill and L. Wyssling prospecting the torque ripple compensation on the field oriented control of the HDrive17. This compensation allows to increase the path accuracy during positioning. The topic was theoretically analyzed in Matlab Simulink and implemented on a HDrive17 Servodrive. Furthermore a laser projector was build to show the improvement while projecting a laser beam along a printed trajectory on a paper. The ripple current compensation is increasing the trajectory accuracy by almost 50% in movements with a velocity at around 50 RPM.
Read moreIntroducing the HDrive17-ETH-i
June 13, 2019
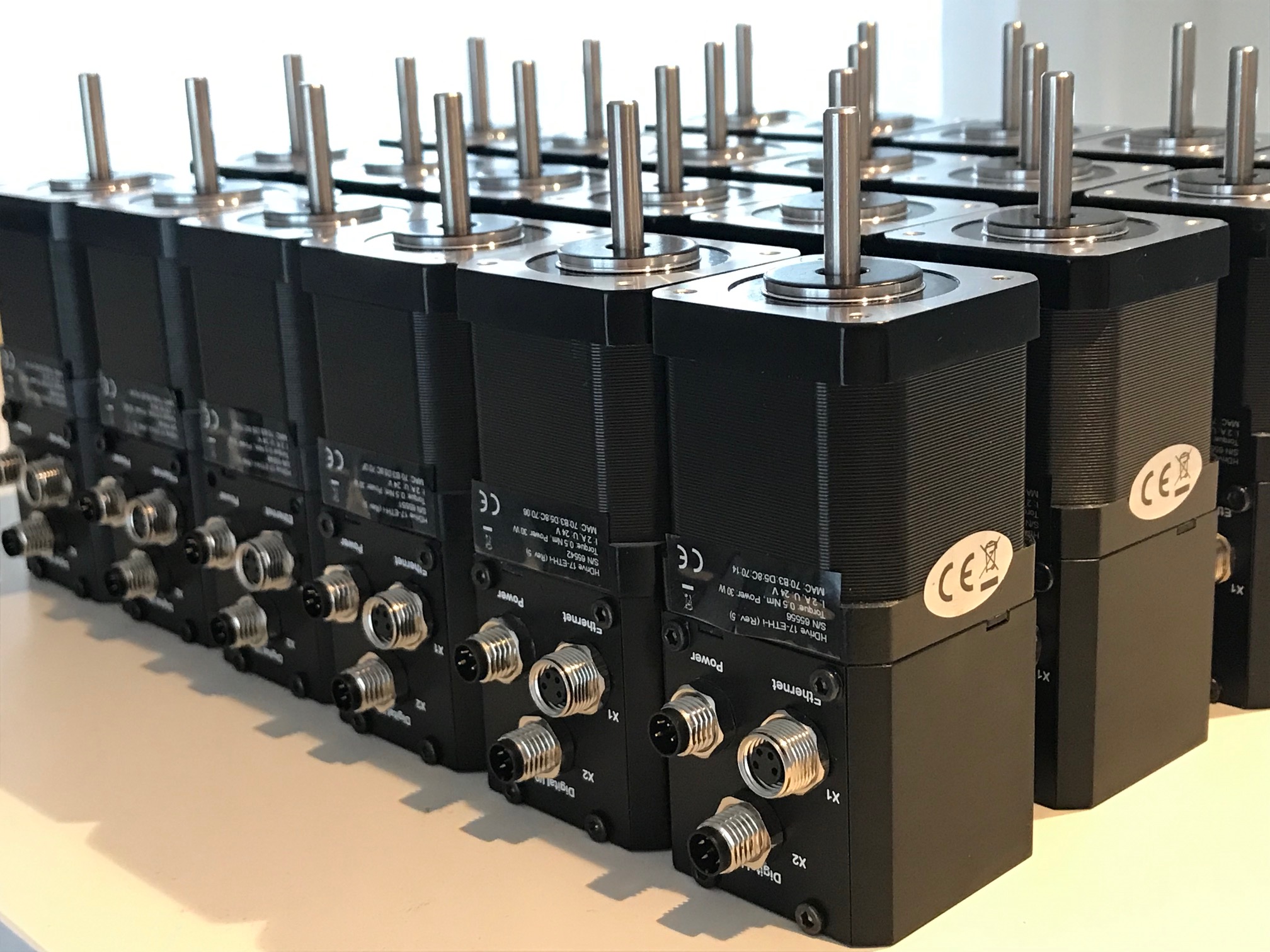
We successfully introduced and already shipped 250 units of the HDrive17-ETH-i (Industrial) servo drive.
Read moreMaker-day!
November 22, 2018
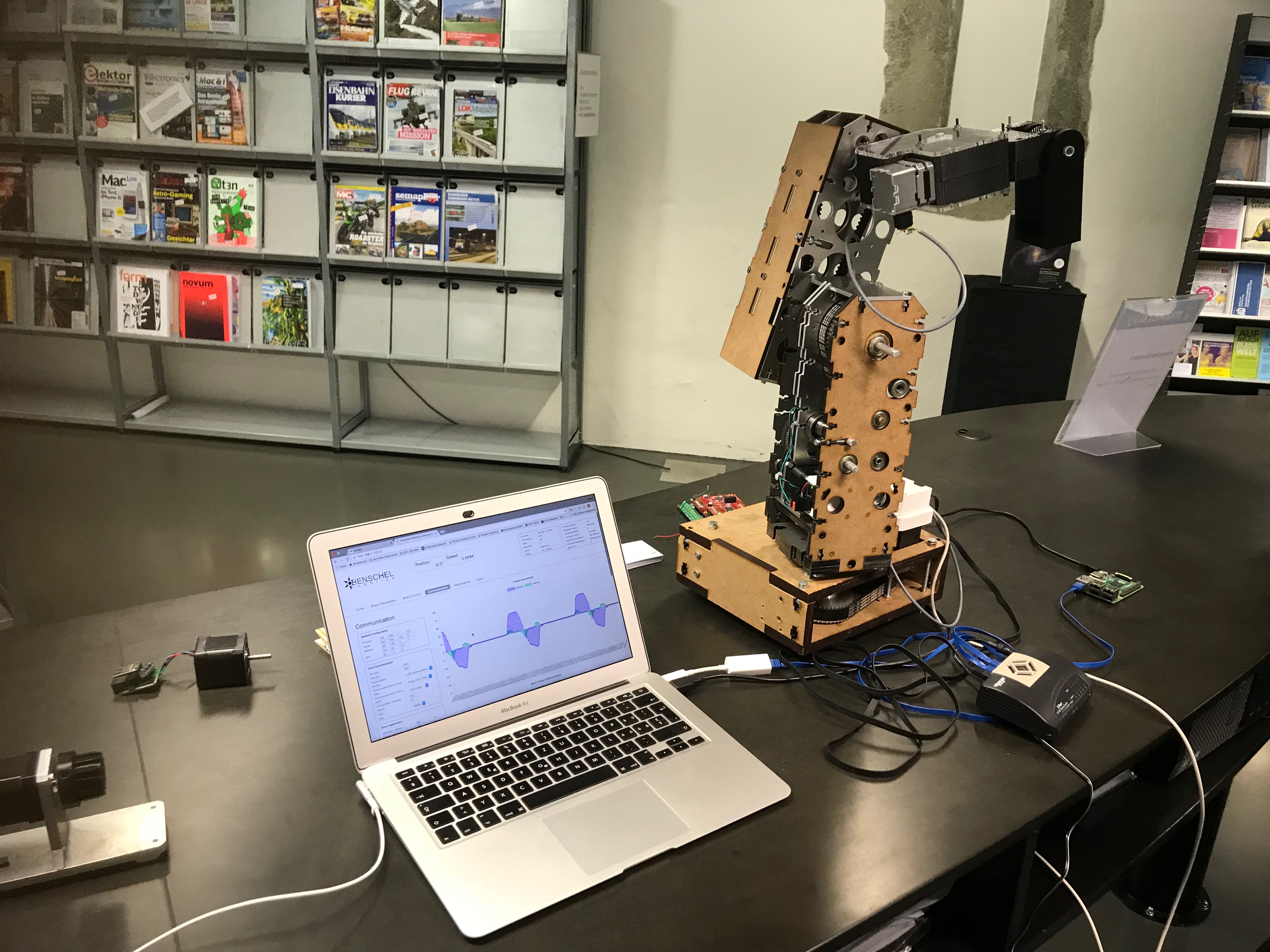
We have been a part of the Maker-day in Winterthur at the Stadtbibliothek Winterthur
Read moreSwiss robotics industry day
November 13, 2018
We have shown our product and a 6-DOF painting robot arm at the Swiss robotics industry day 2018 in Lausanne – again.
Read moreCE Conformity
June 13, 2017
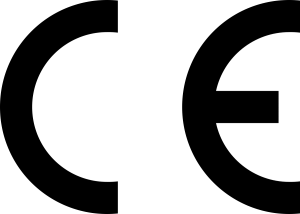
After two days of measurement at Eurofins, we successfully passed EMC/EMI and safety tests. Thanks to the friendly experts in the lab!
Read moreWe started a kick-starter project
November 21, 2016
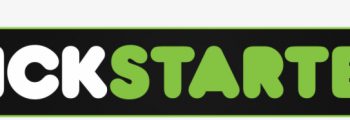
And failed :(, but learned a lot during the campaign about the market need of our product and the target customers. Check out the campaign here.
Read moreSwiss robotics industry day in Lausanne, Switzerland
October 13, 2016
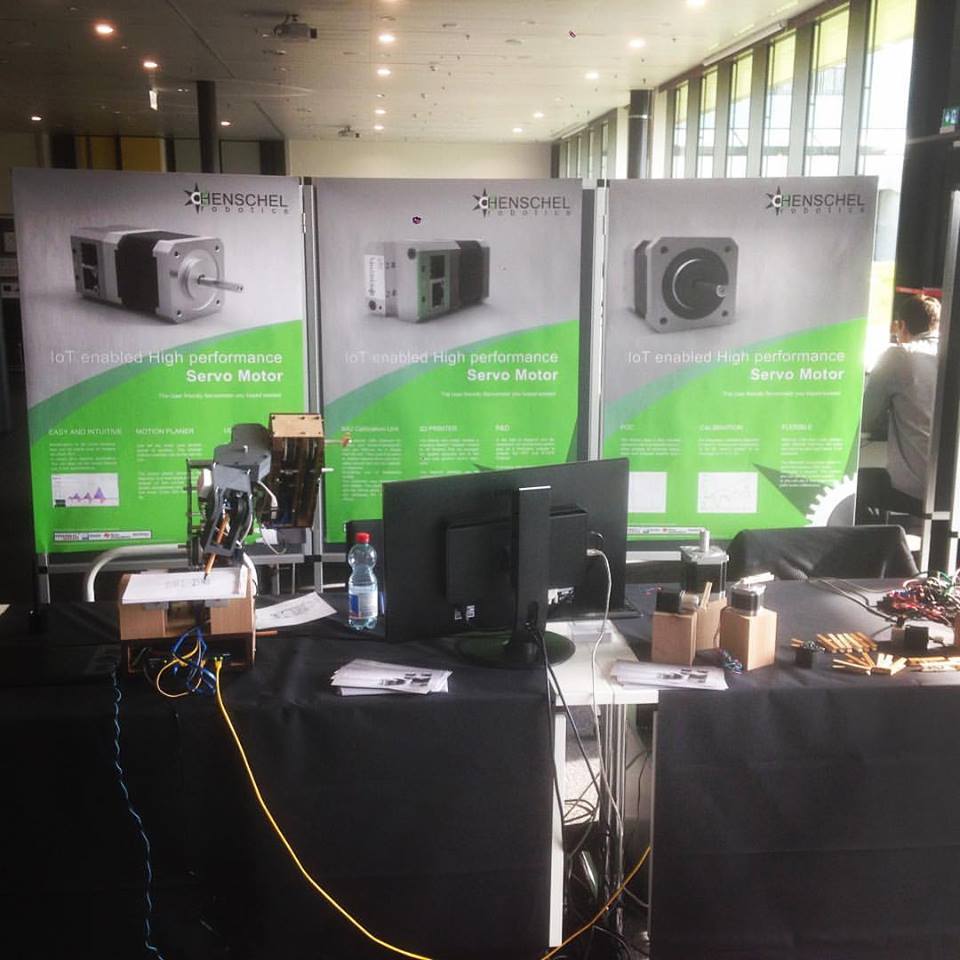
We have shown our product and a 6-DOF painting robot arm at the Swiss robotics industry day 2016 in Lausanne.
Read moreWe showed our product together with our partner Austria Microsystems at the Hannover Messe
June 13, 2015
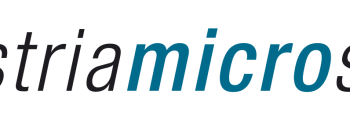
We had the chance to work with Austria Microsystems to exchange the knowledge about magnetic position systems. This teamwork was very successfully and could increase our drive system accuracy significantly. As another benefit we have been invited to share a booth at one of the biggest automation fair in the world.
Read moreVenture kick stage 1.
January 6, 2014
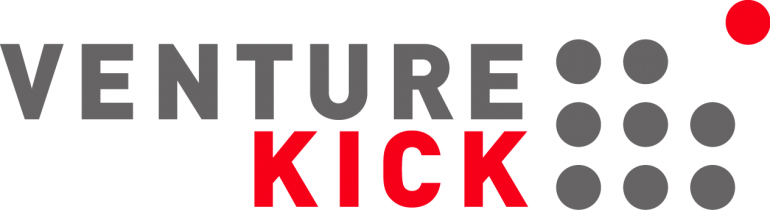
We successfully participated in the Venture Kick stage 1. This gave us the right kick mentally and financally. Thank you VentureKick!
Read moreWe started to develop the first WiFi stepper drive system
June 13, 2013
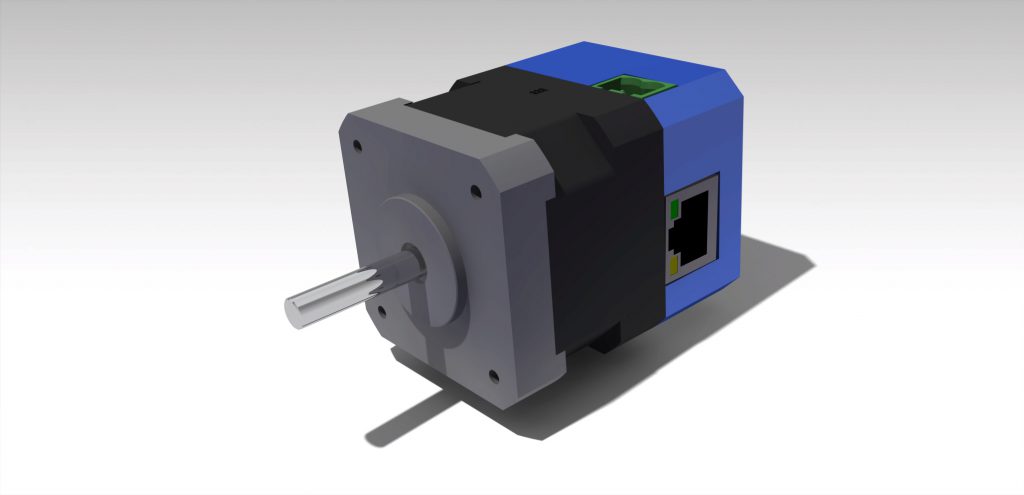
The idea was born during the work on the EU project AVERT. The Mockup should show the motion of a 8 wheeled drive system with mecanum wheels. Thus it should approve the kinematic model for the later product. The control was directly out of a Matlab-Script where the kinematics could be changed or tuned instantly. All motors on the robot have been configured as slaves…
Read more